ตัวอย่าง: MK-G ซีรีส์
ในส่วนนี้จะใช้ MK-G ซีรีส์ จาก KEYENCE เป็นตัวอย่างในการอธิบายโครงสร้างและคุณสมบัติของเครื่องพิมพ์อิงค์เจ็ท
คอนโทรลเลอร์
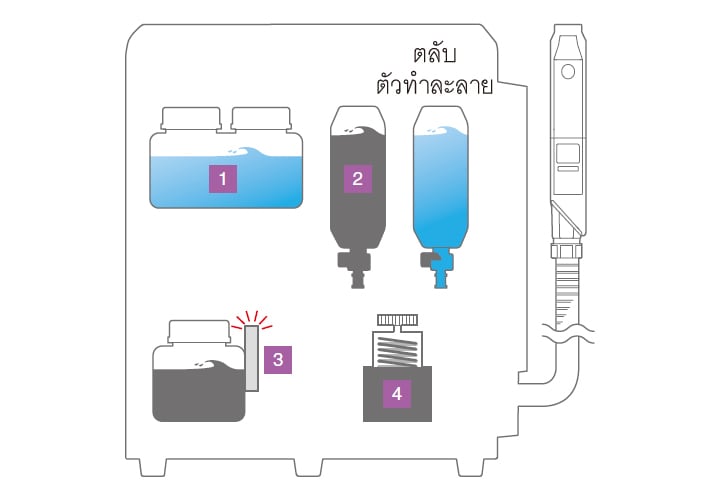
ถังปรับสภาพเทคโนโลยีต้นแบบจาก KEYENCE
ตัวทำละลายที่ใช้ระหว่างการทำความสะอาดโดยอัตโนมัติเมื่อเปิดเครื่อง ปิดเครื่องและ บำรุงรักษาจะถูกเก็บไว้ใน
ถังปรับสภาพ
ถังปรับสภาพนี้จะใช้เพื่อป้องกันไม่ให้หมึกในถังหลักเจือจางและควบคุมความหนืดของหมึก เนื่องจากหมึกเป็นของเหลว
ที่นำไฟฟ้า จึงได้นำเกจวัดระดับที่ใช้อิเล็กโทรดมาใช้เป็นตัวจัดการประจุในถังปรับสภาพ
* โดยทั่วไปแล้วเครื่องพิมพ์อิงค์เจ็ทจะไม่มีถังปรับสภาพ จึงต้องเก็บตัวทำละลายไว้ในถังหลักซึ่งเป็นสาเหตุที่ทำให้หมึกเจือจาง
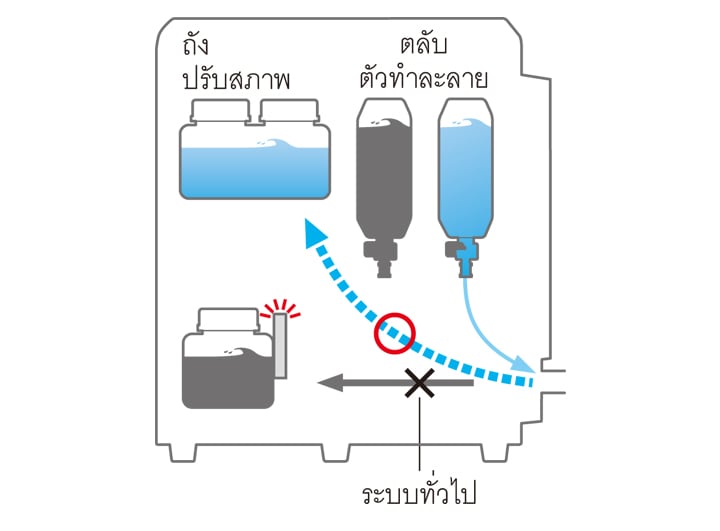
ตลับหมึก
เครื่องพิมพ์จะป้อนหมึกเข้าไปในระบบได้สองวิธี ได้แก่ เติมหมึกเข้าถังหมึกจากขวดหรือ ใส่ตลับหมึก
ข้อดีของการใช้ตลับที่มีชิป IC
- ป้องกันการใส่อุปกรณ์ไม่ถูกต้อง
- หากชนิดของหมึกหรือตัวทำละลายไม่ถูกต้อง ระบบจะแจ้งเตือนข้อผิดพลาดให้ผู้ใช้ทราบ
- สามารถตรวจสอบ ปริมาณคงเหลือได้
- ปริมาณคงเหลือของของเหลวจะแสดงเป็น เปอร์เซ็นต์
- มีเซนเซอร์ตรวจจับความว่างเปล่า
- ใช้ของเหลวในตลับได้อย่างหมดจด
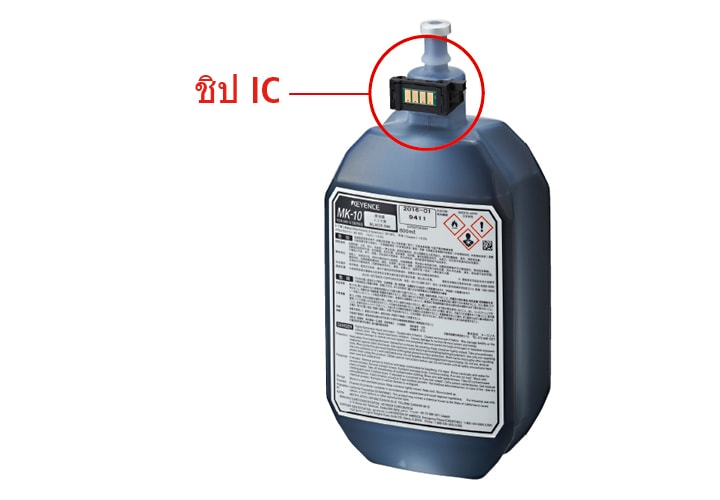
เครื่องวัดความหนืด
เครื่องวัดความหนืดจะตรวจจับความหนืดภายในถังหลักตลอดเวลาเพื่อรักษาความหนืด ที่เหมาะสมไว้ หมึกจากถังหลักจะไหลเข้าสู่เครื่องวัดความหนืดซึ่งข้อมูลจะถูกส่งกลับ เพื่อแก้ไขระดับความหนืด นอกจากนี้ยังวัดอุณหภูมิของหมึกภายในเครื่องวัดความหนืด เพื่อปรับความหนืดให้เข้ากับอุณหภูมิ ที่ระบุด้วย
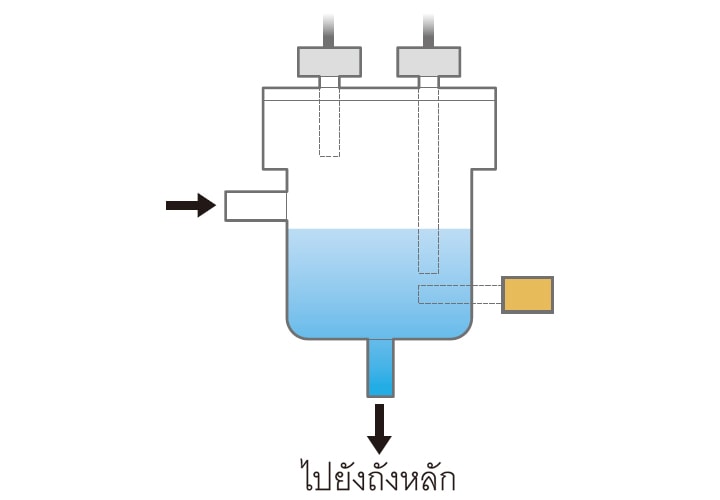
วาล์วลดแรงดัน
แรงดันที่ด้านหลักไม่คงที่เนื่องจากใช้ปั๊ม จึงต้องใช้วาล์วลดแรงดันเพื่อคอยรักษาแรงดันที่ด้านรองให้คงที่
วาล์วลดแรงดัน คือ วาล์วควบคุมแรงดันที่ทำงานเองโดยมีแรงดันจากของเหลวเป็นตัวกระตุ้นการทำงาน หากแรงดันที่
ด้านรองต่ำ ตัวนำร่องก็จะอยู่ต่ำ ทำให้หมึกไหลไปยังด้านรองมากขึ้นและทำให้แรงดันเพิ่มขึ้น ในทางกลับกัน
หากแรงดันสูง ตัวนำร่องก็จะอยู่สูง หมึกจึงไม่ไหลไปยังด้านรองและทำให้ระดับแรงดันคงที่
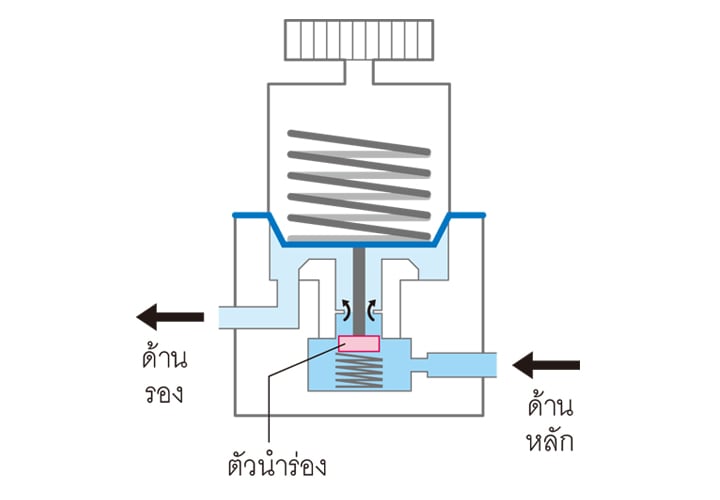
หัวพิมพ์
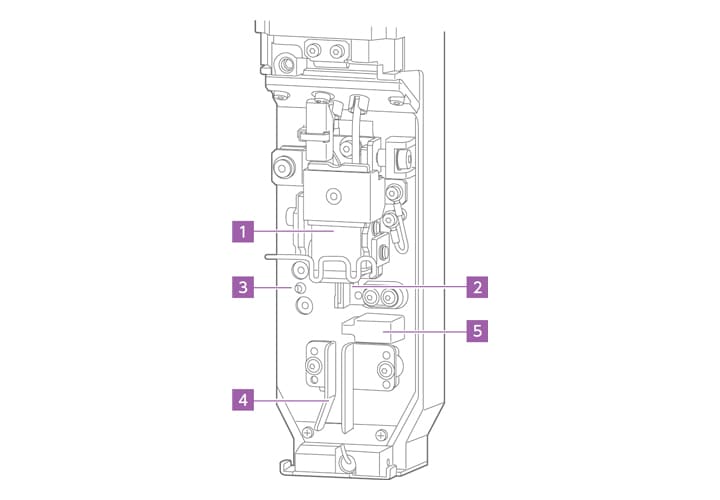
แคนนอน (ส่วนประกอบ Piezo และหัวฉีด)
ภายในแคนนอน ชิ้นส่วนทรงกระบอกที่รูปทรงคล้ายกรวยจะสั่นในแนวขึ้นลง เพื่อสร้างละอองหมึกจากแถวหมึก
ต้นทางการสั่น คือ ส่วนประกอบ Piezo ลักษณะเฉพาะขององค์ประกอบนี้ทำให้เกิดการสั่นสะเทือน ซึ่งปริมาณ
การสั่นจะเปลี่ยนไปเมื่อได้รับแรงดันไฟฟ้า
องค์ประกอบนี้จะเชื่อมต่อกับกรวยและจะสร้างละอองหมึกประมาณ 70,000 อนุภาคต่อวินาที แคนนอนจะมีเส้นทาง
ป้อนหมึกหนึ่งทางและอีกเส้นทางสำหรับเก็บหมึก ในระหว่างการดำเนินการวาล์วโซลินอยด์จะปิดเส้นทางเก็บหมึก
และแคนนอนจะฉีดหมึกออกมาจากหัวฉีด
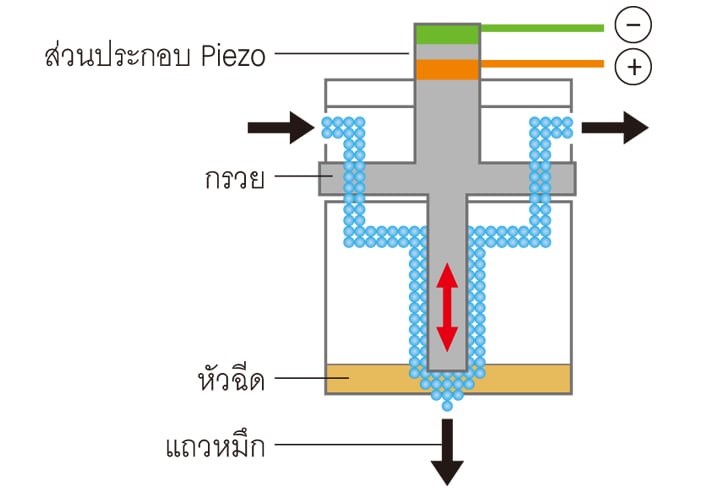
แผ่นอิเล็กโทรดไฟฟ้าสถิต
หัวฉีดจะฉีดหมึกออกมาเป็นแถวผ่านแผ่นอิเล็กโทรดไฟฟ้าสถิต ซึ่งทำให้หมึกแตกออกเป็นละอองหมึกที่เหมาะสมที่สุด
แรงดันไฟฟ้าพัลส์จะส่งแถวหมึกไปยังแผ่นอิเล็กโทรดไฟฟ้าสถิต ปริมาณความอิ่มตัวของประจุไฟฟ้าขั้วลบในแถวหมึก
จะแตกต่างกันไปตามขนาดของพัลส์ ทันทีที่ละอองหมึกก่อตัวขึ้นปริมาณของประจุไฟฟ้าที่แต่ละละอองหมึกได้รับก็จะ
แตกต่างกัน เพื่อให้แต่ละอนุภาคมีแรงดันไฟฟ้าขั้วลบที่สัมพันธ์กับข้อมูลตำแหน่งที่จะพิมพ์
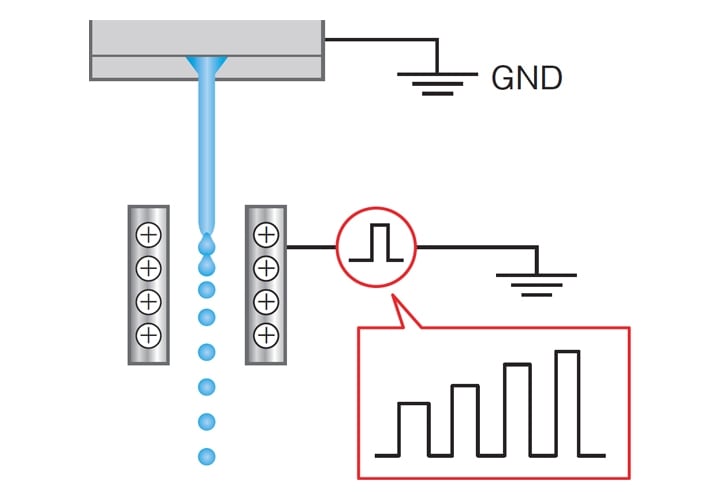
การฉีดตัวทำละลาย อัตโนมัติเทคโนโลยีต้นแบบจาก KEYENCE
หากภายในหัวพิมพ์สกปรกจะทำให้พิมพ์ได้ไม่ถูกต้อง MK-G ซีรีส์ จาก KEYENCE มีฟังก์ชันการทำความสะอาดและ
เป่าแห้งโดยอัตโนมัติ ซึ่งจะฉีดตัวทำละลายด้วยแรงดันสูงใส่หัวฉีด แผ่นอิเล็กโทรดไฟฟ้าสถิต และแผ่นอิเล็กโทรดหักเห
หลังจากทำความสะอาดแล้วภายในของหัวพิมพ์จะถูกเป่าแห้ง
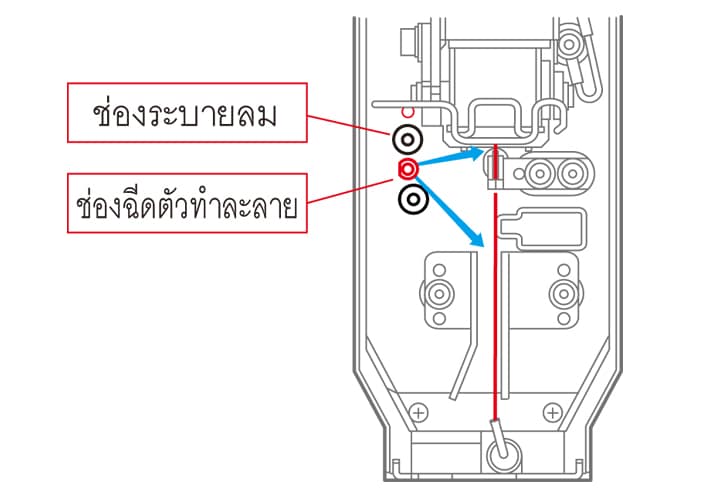
แผ่นอิเล็กโทรดหักเห
แผ่นอิเล็กโทรดหักเหได้รับแรงดันไฟฟ้าสูงทำให้เกิดสนามแม่เหล็ก เมื่อละอองหมึกที่ได้รับประจุไฟฟ้าขั้วลบไหลผ่าน
แผ่นอิเล็กโทรดหักเห ละอองหมึกจะเปลี่ยนทิศทางตามประจุที่ได้รับ
* สนามแม่เหล็กจะเกิดรอบๆ วัตถุที่ได้รับแรงดันไฟฟ้าเสมอ
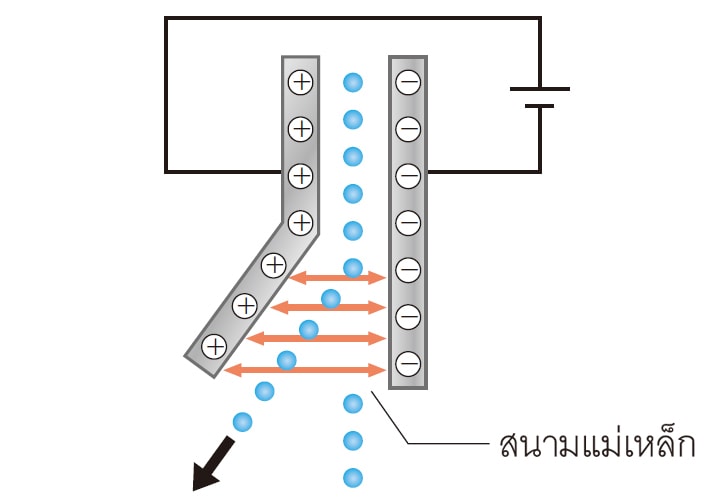
เซนเซอร์ประจุ
การตรวจสอบสถานะของอนุภาค
ความหนืดของหมึกจะเปลี่ยนแปลงตลอดเวลา เมื่อความหนืดของหมึกเปลี่ยน เวลาที่ใช้สร้างละอองหมึกและปริมาณประจุ
ที่ส่งก็จะเปลี่ยนไปด้วย ซึ่งจะทำให้เกิดความบกพร่องขึ้น เช่น ข้อความที่ไม่เสถียร ในกรณีนี้จำเป็นจะต้องปรับแรงดัน
Piezo โดยเมื่ออนุภาคหมึกที่มีประจุไฟฟ้าไหลผ่านเซนเซอร์ก็จะตรวจจับเพื่อปรับประจุไฟฟ้าที่ใช้ให้เหมาะสม
- การปรับละอองหมึกให้เหมาะสม ที่สุดโดยอัตโนมัติเทคโนโลยีต้นแบบจาก KEYENCE
- MK-G ซีรีส์ จาก KEYENCE จะรับรู้ถึงตำแหน่งที่หมึกแตกตัวออกเป็นอนุภาคแล้วปรับแรงดัน Piezo
ระบบจะวัดเมื่ออนุภาคหมึกไหลผ่านเซนเซอร์ประจุ เพื่อกำหนดแรงดันไฟฟ้า โดยทั่วไปแล้วจะต้อง
ปรับแรงดัน Piezo ด้วยตนเอง
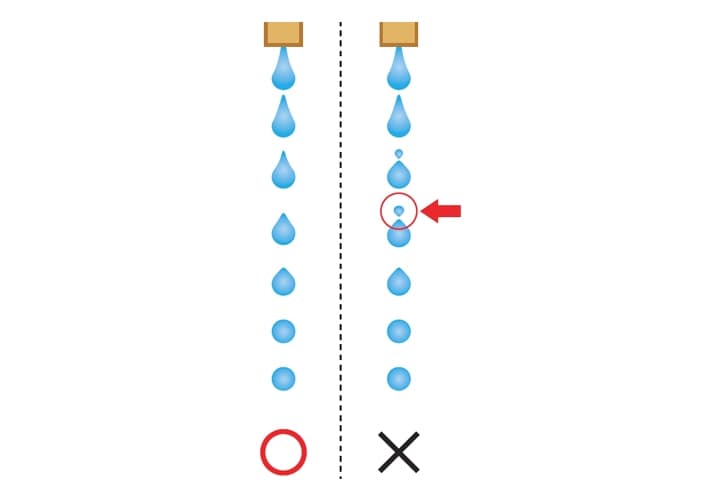
